Introduction to Embodied Carbon for Advanced Building Construction
The Basics of Embodied Carbon Measurement, Reduction, and Reporting
Authors: Audrey Rempher, Rebecca Esau
About This Guide
This guide is an introductory resource for building product manufacturers who would like to reduce embodied carbon in their products. The navigation bar allows users to explore different sections and learn the basics of how to measure, reduce, and report embodied carbon for building materials and products. The guide also includes a glossary of common embodied carbon terms for reference.
This resource was inspired and informed by monthly convenings of the Embodied Carbon Working Group hosted by the Advanced Building Construction (ABC) Collaborative in 2021–2022. The participants, representing organizations ranging from material and product manufacturers to nonprofit and academic groups, identified barriers to reducing embodied carbon in building construction products. One of the key industry challenges identified by this group was the need for foundational information to help navigate embodied carbon reporting and reduction methods.
What Is Embodied Carbon?
In the buildings sector, embodied carbon refers to the greenhouse gas (GHG) emissions associated with the manufacturing, transportation, installation, maintenance, and disposal of building materials, which can be significant — these currently account for approximately 28 percent of the average annual global buildings-related emissions. Embodied carbon does not include the carbon emissions associated with the operation of a building (e.g., from on-site fossil fuel combustion or electricity generation). Embodied carbon is calculated as global warming potential (GWP) and expressed in carbon dioxide equivalent units (CO2e).
Embodied Carbon in Advanced Building Construction
Advanced building construction uses industrialized construction, innovative building technologies and materials, and streamlined processes and project delivery approaches to deliver high-quality buildings and retrofits with reduced GHG footprints. By employing industrialized processes and production methods such as prefabrication, 3-D printed building components, and designing for replicability and volume, buildings can be constructed or retrofitted rapidly and at scale, often with less material waste and sometimes with reduced overall construction costs.
As demand for industrialized production methods grows, builders are simultaneously looking for ways to reduce the environmental impacts of their activities, including the carbon embodied in building materials. The majority of embodied carbon in buildings comes from emissions that occur during material and product manufacturing, including raw material supply and extraction, transport to processing and manufacturing facilities, and manufacturing activities. For example, for typical low- and mid-rise homes in the United States, 65–80 percent of total embodied carbon emissions come from producing building materials. As builders aim to reduce these emissions, manufacturers are leveraging low-embodied-carbon materials and practices to stay competitive.
Applying ABC approaches inherently impacts the embodied carbon of a project. Industrialized production methods increase efficiency and control in the manufacturing of assemblies and packaged products, resulting in more efficient material use and less waste, improved capacity to make critical design changes that affect embodied-carbon outcomes, and shortened production and construction timelines resulting in less on-site energy use and fuel consumption.
Benefits of Lowering Your Product’s Embodied Carbon
Reducing the embodied carbon of a product can bring numerous benefits, including:
- Increased Sales and Competitive Advantage: Gain a competitive advantage as consumer demand for low-embodied-carbon products grows.
- Policy Compliance: Ensure compliance with current or future federal, state, and municipal low-embodied-carbon procurement regulations such as the Federal Buy Clean Initiative.
- ESG Publicity: Demonstrate your commitment to more sustainable products to improve your company’s valuation and increase stakeholder and investor satisfaction.
- Health and Wellness: Incorporate natural materials as a visible design feature to add value for customers. Studies show timber and other natural products that can have low embodied carbon are correlated with healthy and productive environments when visible to occupants.
How is embodied carbon measured?
Quantifying embodied carbon requires a methodology called life-cycle assessment (LCA). LCAs calculate various environmental impacts of a product, building, or process over various life-cycle stages, from raw material extraction through manufacturing and end-of-life disposal or recycling. LCAs use a variety of metrics, including global warming potential. Other metrics measured through LCA can include acidification potential, eutrophication potential, smog formation potential, and ozone depletion potential.
In building construction, LCAs are performed at two levels: building-level LCAs and product- or material-level LCAs. Building-level LCAs, often referred to as whole-building LCAs, provide an assessment of the embodied carbon impact of an entire building. This assessment includes the impact of all materials and products used in the project, or a portion of the project, throughout the life cycle of the building.
Product-level LCAs assess the environmental impacts of an individual material or assembly, such as insulation, window assemblies, or concrete masonry units. Product-level LCAs are commonly conducted as “cradle-to-gate” studies, where “cradle” refers to the sourcing of raw materials and “gate” refers to the factory exit gate; however, they can be expanded to include impacts from maintaining or disposing of the product once it has reached the end of its useful life. LCA studies can be used to track supply chain–specific data and compare functionally equivalent materials or components, allowing manufacturers to make informed decisions regarding their product design and manufacturing processes.
The results of a cradle-to-gate product-level LCA can be summarized and communicated via an environmental product declaration (EPD). EPDs are independently verified documents based on international standards that report certain environmental impacts of a product and typically do not disclose the proprietary information needed to conduct the LCA itself.
Embodied carbon–focused procurement policies for construction projects are quickly spreading across North America. These policies require the disclosure of a construction product or material’s GWP as stated in a product-specific and third-party-verified EPD. To learn more about EPDs, navigate to section 4: Reporting Embodied Carbon.
The Benefits of Conducting a Product-level LCA
Conducting a product LCA can provide valuable data for business decisions beyond the assessment of the environmental impact of a product, such as:
- Product Design: Use LCAs as a design tool to gain insight into opportunities to reduce embodied carbon in products. Conduct iterative LCAs throughout the design phases to refine processes and components that affect a product’s environmental impact. Compare LCA data against a baseline or with other products on the market to determine if the product meets certain requirements or has a competitive edge.
- Procurement: Conduct LCAs to identify and address embodied carbon hotspots along a product’s supply-chain.
- Marketing & Sales: Publish EPDs to ensure products are included in the selection process for purchasers complying with public or private low-embodied-carbon procurement policies. Use LCA data and insights to communicate a product’s unique value to customers.
- ESG Reporting: Include LCA data in environmental, social, and governance (ESG) reporting to demonstrate your commitment to more sustainable products and improve your company’s valuation.
Understanding Life-cycle Stages
For LCA calculations, a building or product’s life cycle is divided into five stages and seventeen modules, as noted below in Exhibit 1:
- Product Stage (A1–A3): including raw material supply, transport, and manufacturing
- Construction Process Stage (A4–A5): including transport and construction installation
- Use Stage (B1–B7): including use, maintenance, repair, and replacement (note: the Use Stage encompasses operational energy use, still the largest driver of buildings-related GHG emissions on average)
- End-of-Life Stage (C1–C4): including demolition and deconstruction, transport, waste processing, and disposal
- Reuse, Recovery, and Recycling Potential (D)
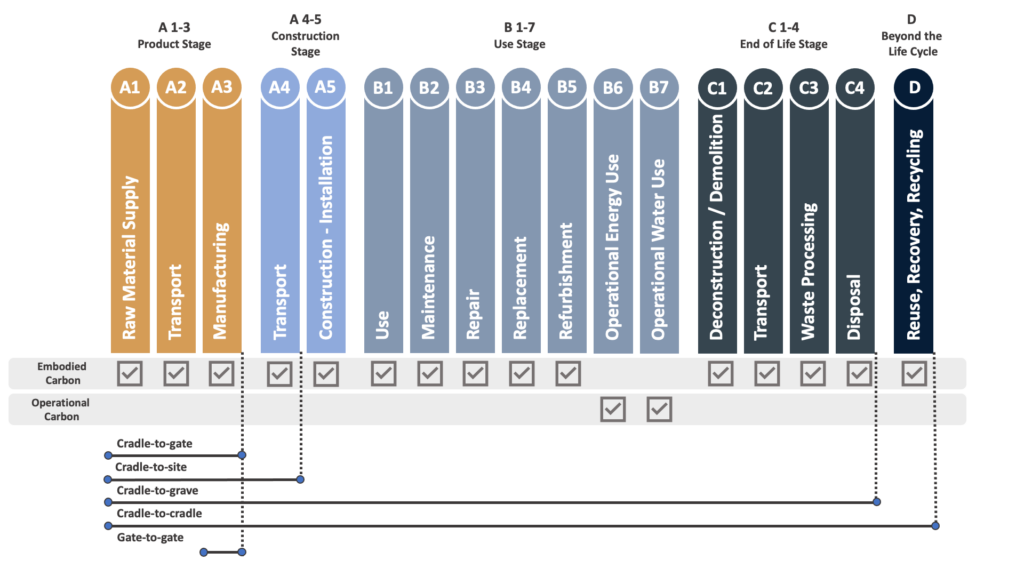
The Different Life-cycle Boundary Conditions
To define what is included in an LCA study, there are five typical boundary conditions to choose from:
- Cradle-to-gate (A1–A3): “Cradle” refers to the sourcing of raw materials and “gate” refers to the manufacturing exit gate. Cradle-to-gate only accounts for a product’s impact until it leaves the factory bound for a distributor, buyer, or consumer. A cradle-to-gate assessment is the model most often used in EPDs for individual building products.
- Cradle-to-site (A1–A4): Cradle-to-site analysis is a variation of the cradle-to-gate analysis that includes impacts from transporting materials and products to the construction site.
- Cradle-to-grave (A1–C4): A cradle-to-grave analysis includes a product’s impact across all five stages of a product’s life cycle.
- Cradle-to-cradle (A1–D): Cradle-to-cradle is a variation of a cradle-to-grave analysis, substituting a recycling process for the waste stage.
- Gate-to-gate (A3 only): Gate-to-gate analysis is from factory entry gate to factory exit gate and considers only the manufacturing process, excluding the raw material supply chain and the product’s use and disposal.
Conducting an LCA
There are several software tools available to assist in performing a product-level LCA including SimaPro, OpenLCA, and Sphera. Some third-party service providers that offer services to develop product-level LCAs include but are not limited to: ICC Evaluation Service, WAP, Intertek, and Anthesis (note that the ABC Collaborative does not specifically endorse any LCA service providers).
LCAs consist of four phases (defined in the ISO standards 14040 and 14044):
1. Goal and Scope
Before conducting the analysis, the scope and goals of the assessment must be defined:
- Reason for Conducting the LCA: For example, a goal could be to benchmark a product’s embodied carbon performance using third-party benchmarks or a baseline product.
- Functional Description: Identify the technical requirements, which are typically defined by codes, standards, and rating systems, and the expected service life of the product.
- Reference Unit: Define the functional unit for your product. For example, the impacts of a wall panel or flooring would commonly be measured per square meter of panel/product area.
- Reference Study Period: Define the temporal boundary of the assessment, typically measured in years.
- System Boundary: Determine which product or portion of the product will be assessed, which product life-cycle stages will be included, and which environmental impacts will be evaluated.
2. Life-cycle Inventory
This is the data collection phase of the assessment, during which a life-cycle inventory (LCI) analysis is conducted to quantify the environmental inputs and outputs of the system defined in Phase 1. Potential inputs and outputs for a product may include:
- Raw materials
- Energy use (e.g., for extraction, processing, etc.)
- Transportation fuel
- Water use
- Waste material
Although many pieces of necessary data may be available from a producer’s records, this analysis can be elaborate due to the complexity of production processes and supply chains.
The quality of the LCA results depends on the LCI data used for the analysis. Once the data is collected, an inventory flow model is used to model the LCI and illustrate the system, inputs, and outputs of the analysis.
3. Impact Assessment
To complete the assessment, the LCI data from Phase 2 is used to calculate the environmental impact of the product. This is done by multiplying the LCI data by appropriate environmental impact factors for each data point and summing to determine a total for each impact category included in the analysis.
The most common LCA impact categories include:
- Global warming potential (GWP)
- Acidification potential (AP)
- Eutrophication potential (EP)
- Photochemical ozone creation potential (POCP)
- Ozone depletion potential (ODP)
When several types of emissions contribute to one LCA impact category, the category is measured in equivalents (denoted as “e” or “eq”). For example, CO₂e is used for GWP because multiple emission types, including methane and nitrous oxide, contribute to GWP in addition to CO₂. To consolidate all contributing gases into one indicator, all are converted to CO₂e.
4. Interpretation
In the final phase of the assessment, the results from Phase 3 are interpreted to draw conclusions and develop recommendations.
This phase of the LCA should:
- Identify any significant issues based on the LCI phase
- Evaluate the level of completion and consistency of the assessment
- Define limitations and conclusions of the assessment
- Develop recommendations for modifications to the product or manufacturing process
Interpretation of the LCA results can provide valuable insights into the product, such as:
- How high are the emissions of the product?
- Are most emissions coming from a specific input or process along the supply chain, or are they spread out?
- Which materials contribute the most to the product’s embodied carbon impact?
- What are the biggest leverage points to reduce the impact of the product?
- How does the impact of the product compare to other products on the market?
- How can the manufacture of the product be more energy efficient?
Opportunities to reduce embodied carbon occur throughout the design and manufacturing process. Exhibit 2 lists strategies and accompanying actions that manufacturers can take to minimize the embodied carbon of their products throughout each stage of production.
Exhibit 2: Strategies and accompanying actions to minimize embodied carbon.
STRATEGIES | ACTIONS | |
Design | Life-cycle Assessment |
|
Material Efficiency |
| |
Material Selection |
| |
End-user Considerations
|
| |
End-of-Life Considerations |
| |
Manufac-turing | Plant Energy Efficiency |
|
Energy Use |
| |
Reuse and Recycling |
| |
Installati-on | Transportation |
|
Construction |
|
Environmental Product Declarations
Environmental product declarations (EPDs) are independently verified documents that report the environmental data from a life-cycle assessment (LCA) in accordance with international standards. EPDs are often referred to as a “nutrition label” for building products because they report a variety of life-cycle impacts, including GWP, acidification, eutrophication, ozone depletion, and smog formation. EPDs can also include additional manufacturer and product data, such as materials, manufacturing processes and locations, and resource use. EPDs are intended to be published for consumers to review and are valid for up to five years.
EPDs are governed by product category rules (PCRs), which dictate how practitioners should perform the LCA for an EPD of a given product category. PCRs establish reporting requirements, system boundaries, and the functional unit. ISO standards dictate that PCR development must involve participation from a range of stakeholders as well as a public comment and review process. PCRs expire and must be reviewed and updated every five years at a minimum.
How Are EPDs Used?
EPDs are the predominant tool for embodied carbon disclosure and transparency in the building construction industry. EPDs are used to track supply chain-specific product data and to compare the environmental impacts of functionally equivalent products. Functionally equivalent products are products intended to be used for the same purpose and must have the same LCA scope to allow comparison.
Policies targeting the reduction of carbon emissions associated with building products require the disclosure of embodied carbon data via EPDs to verify whether reduction targets have been met.
The Different Types of EPDs
Industry-wide EPDs: Industry-wide EPDs represent average manufacturing impacts for a product from multiple manufacturers within a geographic region. Industry-wide EPDs are typically published by trade associations and based on data from member manufacturers. Because industry-wide EPDs disclose average data, they provide a useful benchmark that can be used to set targets for policy, or for manufacturers seeking to reduce the embodied carbon of their product relative to a general baseline.
Product-specific EPDs: Product-specific EPDs represent the impacts for a specific product from a single manufacturer and are used to compare functionally equivalent products.
Facility-specific EPDs: Facility-specific EPDs are product-specific EPDs in which the environmental impacts can be attributed to a single manufacturer and manufacturing facility. Facility-specific EPDs capture the unique grid mix and fuel sources used in a single manufacturing facility.
How to Create an EPD
To create an EPD, a product manufacturer must engage with a third-party service provider to conduct a life-cycle assessment for the product. The process typically includes:
- Data collection: The service provider collects data on the inputs to the product, energy consumption for production, and chemical process emissions.
- Life-cycle assessment (LCA) and EPD report generation: The service provider must follow designated ISO standards as well as PCRs, which spell out a predetermined set of requirements and guidelines for conducting an LCA. See conducting an LCA section above for more information.
- Verification and publication: Once generated, the EPD is verified by a third party and made available to the public.
- Expiration: EPDs expire after five years and must be renewed using current data and protocols.
Barriers to EPD Standardization and Adoption
Although the number of product and material EPDs is growing rapidly, several barriers to EPD standardization and adoption remain, including:
Up-front costs to set up with an EPD service provider can be prohibitive for some small business enterprises.
- EPD development is often out of sync with PCRs, which expire every five years, affecting the validity of EPDs.
- Inconsistencies in EPD development result in non-comparable data. For example, non-facility-specific EPDs using industry average values across multiple facilities will not be as accurate as EPDs developed using facility-specific data.
- Without a universal public database to reference, different EPD-generating software pull from different proprietary background datasets, resulting in different estimates for the same product.
- There is a lack of industry-wide EPDs for certain types of products, making material or product GWP baselining difficult.
LCA professionals and academics, nonprofit organizations, and government bodies recognize the need to address these barriers. The federal Inflation Reduction Act of 2022 provides significant funding for the advancement of EPDs, including the establishment of an EPD Assistance Program and a low-embodied-carbon labeling system for construction materials.
Glossary
Term | Definition |
Biomass | Material of biological origin excluding material embedded in geological and/or fossilized formations.
|
Boundary conditions | Used to define what is included in a life-cycle assessment (LCA) study. The most common boundary conditions are cradle to gate, cradle to site, and cradle to grave. |
Carbon dioxide equivalent (CO2e) | A measure used to compare the impact of various greenhouse gases (GHGs) based on their global warming potential (GWP). CO2e approximates the time-integrated warming effect of a unit mass of a given GHG relative to that of carbon dioxide (CO2). The following GWP values are commonly used based on a 100-year time horizon: 1 for CO2, 25 for methane (CH4), and 298 for nitrous oxide (N2O).
|
Carbon footprint | The total amount of greenhouse gas (GHG) emissions associated directly and indirectly with a product, building, individual, organization, or event. Carbon footprint is measured in carbon dioxide equivalent units (CO2e), commonly expressed as global warming potential (GWP).
|
Carbon offset | Emissions reductions or removals achieved by one entity that can be used to compensate for (offset) emissions from another entity. |
Carbon sequestration | The process of capture and long-term storage of atmospheric carbon dioxide (CO2) in durable, mineral form.
|
Carbon storage | The process of capturing and durably storing atmospheric carbon dioxide (CO2) via photosynthesis in biomass materials. |
Cradle to cradle | A boundary condition associated with embodied carbon, carbon footprint, and life-cycle assessment (LCA) studies. The boundary includes all activities starting with the extraction of materials (the cradle), their transportation, manufacturing, delivery and installation, use and maintenance, disassembly, and reuse or recycle potential (life-cycle modules A1 through D).
|
Cradle to gate | A boundary condition associated with embodied carbon, carbon footprint, and life-cycle assessment (LCA) studies. The boundary includes all activities starting with the extraction of materials (the cradle), their transportation, and the manufacturing activities that prepare the material or product to leave the factory gate (life-cycle modules A1 through A3).
|
Cradle to grave | A boundary condition associated with embodied carbon, carbon footprint, and life-cycle assessment (LCA) studies. The boundary includes all activities starting with the extraction of materials (the cradle), their transportation, manufacturing activities, delivery, installation, use and maintenance, disassembly, and disposal (life-cycle modules A1 through C4).
|
Cradle to site | A boundary condition associated with embodied carbon, carbon footprint, and life-cycle assessment (LCA) studies. The boundary includes all activities starting with the extraction of materials (the cradle), their transportation, manufacturing activities, and delivery to the construction site (life-cycle modules A1 through A4).
|
Embodied carbon | The greenhouse gas (GHG) emissions arising from the manufacturing, transportation, installation, maintenance, and disposal of building materials.
|
End-of-life carbon | The greenhouse gas (GHG) emissions associated with deconstruction and demolition, transport from site, waste processing, and disposal phases of a building material’s life cycle (life-cycle modules C1-C4).
|
Environmental product declaration (EPD) | Defined by ISO 14025 as a Type III declaration that “quantifies environmental information on the life cycle of a product to enable comparisons between products fulfilling the same function.” EPDs provide environmental data based on a life-cycle assessment (LCA) conducted in accordance with the designated product category rule (PCR) and report a variety of life-cycle impacts such as global warming potential (GWP), acidification, eutrophication, ozone depletion, and smog formation.
|
Global warming potential (GWP) | An index for estimating the relative global warming contributions of GHG emissions expressed in carbon dioxide equivalent units (CO2e), commonly referred to as a carbon footprint. |
Industry-wide EPD | A disclosure of the environmental impacts of a range of individual products from a group of manufacturers. Industry-wide EPDs represent typical manufacturing impacts for a type of product but are not specific to any one individual product. |
Life-cycle assessment (LCA) | A scientific methodology used to calculate the environmental impacts, including carbon footprint, of a product, service, or process.
|
Material passports | A digital document containing a detailed inventory of all the materials or components used in a building and their location to encourage material recovery and reuse after a building has reached the end of its useful life.
|
Net-zero carbon building | A building in which the sum of all greenhouse gas (GHG) emissions, both operational and embodied, over a building’s life cycle are eliminated or are minimized and equal zero with offsets for residual emissions.
|
Net-zero embodied-carbon building | A building in which the sum of embodied greenhouse gas (GHG) emissions over a building’s life cycle are eliminated or are minimized and equal zero with the use of carbon sequestering materials or offsets for residual emissions.
|
Net-zero operational-carbon building | A building in which the sum of operational greenhouse gas (GHG) emissions over a building’s life cycle are eliminated or are minimized and equal zero with offsets for residual emissions.
|
Operational carbon | The greenhouse gas (GHG) emissions arising from operating a building, including heating, cooling, ventilation, lighting, plug loads, water use, etc. |
Product category rule (PCR) | Defines the rules and requirements for developing Type III EPDs for a group of products that fulfill an equivalent function. |
Product-specific EPD | A disclosure of the environmental impacts for a specific product and manufacturer across multiple facilities.
|
Scope 1 emissions | Direct greenhouse gas (GHG) emissions that occur from sources that are controlled or owned by the reporting organization. |
Scope 2 emissions | Indirect greenhouse gas (GHG) emissions associated with the production of energy that a reporting organization purchases. |
Scope 3 emissions | Indirect greenhouse gas (GHG) emissions associated with the reporting organization’s value chain. These emissions are not produced by the company itself and are not the result of activities from assets owned or controlled by the reporting organization. Scope 3 emissions include all sources not within an organization’s Scope 1 and 2 boundaries.
|
Upfront carbon | The greenhouse gas (GHG) emissions associated with the raw material supply, transport, manufacturing, and delivery of a building material or product to the construction site (life-cycle modules A1–5).
|
Whole-building life-cycle assessment (WBLCA)
| A life-cycle assessment (LCA) performed on a whole building; See life-cycle assessment for additional information.
|
Whole-life carbon | Emissions from all life-cycle stages, encompassing both embodied and operational carbon together (i.e., modules A1 to C4, with module D reported separately). |